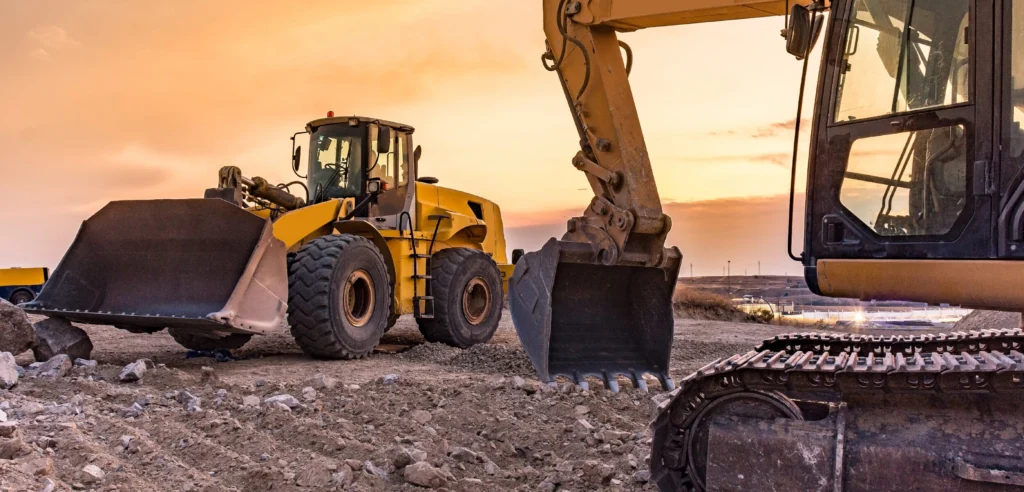
Accurately estimating equipment costs is one of the most critical components of a successful construction bid. Misjudging these expenses can derail your budget, cut into profits, or even lose you the job altogether. This guide on how to estimate equipment cost in construction provides a step-by-step breakdown for contractors, estimators, and project managers to ensure your heavy equipment budgeting is realistic, reliable, and rooted in actual data. Whether you’re planning to buy, rent, or lease, understanding the full picture of equipment costs gives you a competitive edge on every bid.
Why Pricing Equipment into the Budget Matters
Understanding how to estimate equipment cost in construction goes beyond simple line items. Equipment costs directly affect jobsite productivity, timelines, and profitability. Overestimating these costs might inflate your bid and price you out of contention, while underestimating can erode profit margins, delay work, or force unexpected change orders.
Accurate pricing equipment into the job allows for smoother planning and allocation of resources. It also helps improve forecast accuracy across project stages, from preconstruction to closeout. By properly accounting for these expenses upfront, you reduce the risk of unforeseen financial strain and increase your odds of successful project execution.
Key Factors That Impact Equipment Costs
When estimating equipment costs, several variables come into play. From excavators and dumpsters to lulls and cranes, you want to consider the impact of operations and ownership.
Equipment Acquisition Costs
- Purchase Price: The upfront cost of buying new or used equipment.
- Financing: Interest rates and loan terms if financing the purchase.
- Leasing: Monthly rental or lease payments if renting equipment instead of purchasing.
Operating Costs
- Fuel Consumption: The cost of fuel required for daily operation.
- Maintenance & Repairs: Routine servicing, wear-and-tear repairs, and unexpected breakdown costs.
- Operator Wages: The cost of hiring skilled operators to run the equipment.
Depreciation & Resale Value
- Equipment loses value over time, impacting overall project cost. Understanding resale value helps calculate long-term cost efficiency.
Utilization Rate
- How often the equipment will be used during the project. Low utilization can lead to higher per-unit costs.
Jobsite Conditions
- Site terrain and weather can affect fuel efficiency, wear and tear, and overall equipment performance.
Production Costs
Every piece of machinery carries embedded production costs—the materials, labor, and engineering that go into its creation. These factors affect the market price and should be considered when budgeting for purchasing or leasing equipment. High-tech machines with advanced features may command higher prices but could lead to better efficiency and long-term savings.
Supplier Costs
Not all suppliers are equal. Supplier cost can vary depending on brand reputation, geographic location, shipping fees, and inventory availability. Local suppliers may reduce transport costs, while larger dealers might offer better warranty packages or financing options. Always compare multiple quotes before committing.
Operating Costs
Recurring maintenance costs, fuel usage, tires or tracks, and operator wages can add up quickly. These operating costs often exceed the initial purchase price over time. Building these into your estimates gives you a more complete picture of actual expenses.
Depreciation & Resale Value
Heavy machinery loses value with use. While depreciation is inevitable, considering resale value can help offset the total cost over time. Estimating resale or trade-in potential improves lifecycle budgeting and prevents overpaying for equipment with low long-term value.
Utilization Rate
If equipment is used infrequently or across fewer projects, its per-use cost increases. Estimating the utilization rate helps allocate equipment costs appropriately and guides decisions about whether to rent or purchase.
Jobsite Conditions
Terrain, climate, and job duration impact what equipment you need and how often you’ll perform maintenance. Harsh environments may require specialized machinery or increase production and maintenance costs, making accurate estimation even more essential.
Best Practices for Estimating Costs of Construction Machinery
A well-structured equipment cost estimate ensures better budget management and enhances the overall efficiency of project execution. Contractors can make more informed financial decisions and reduce the risk of cost overruns by:
Using Historical Data
Looking at past projects’ equipment costs can provide valuable benchmarks. This historical data helps identify trends, spot common overruns, and create more predictable future estimates.
Considering Lifecycle Costs
Don’t just look at the upfront investment—factor in total ownership costs over time, including maintenance cost, downtime, insurance, and depreciation. This big-picture thinking leads to smarter purchasing and rental decisions.
Accounting for Contingencies
Things go wrong. Equipment breaks down. Fuel prices spike. Building a contingency buffer—usually 5-10% of your total estimate—can prevent budget blowouts when unforeseen equipment costs arise.
Leveraging the Right Technology
Modern estimating platforms like STACK automate calculations, track changes, and reduce manual entry errors. STACK’s tools integrate cost databases, job history, and custom formulas to improve how you price equipment and manage costs in real time.
Renting vs Buying Equipment
Sometimes it’s smarter to rent. For short-term use or highly specialized machinery, renting may reduce your production cost and eliminate repair expenses. Long-term, frequently used equipment is often better bought. Evaluating this trade-off is crucial to getting accurate estimates and optimizing your construction equipment strategy.
How STACK Simplifies Equipment Cost Estimating
STACK allows contractors to efficiently manage preconstruction processes with flexible and accurate estimating. With STACK’s Estimating Worksheet, you get:
- Customizable Cost Breakdowns – Tailor your estimating worksheet to include equipment costs, factoring in purchase, rental, fuel, labor, and maintenance expenses.
- Real-Time Cost Adjustments – Modify estimates on the fly to accommodate changing costs or project conditions.
- Integration with Takeoff & Estimating Data – Ensure seamless calculations by integrating your equipment costs with overall material and labor estimates.
- Cloud-Based Collaboration – Work from anywhere with secure access to your data.
FAQs About the Costs of Construction Equipment and Machinery
Is renting or buying equipment more cost-effective?
It depends on project duration and usage. For short-term or infrequent needs, renting often lowers your equipment costs. For long-term use, purchasing may be more cost-effective in the long run.
How often should I update my equipment cost database?
Ideally, review and update your data quarterly. Changes in supplier rates, fuel prices, or maintenance costs can impact your bottom line.
What are the hidden costs in equipment ownership?
Hidden costs may include insurance, storage, idle time, and unplanned repairs. Factoring these into your production cost estimates improves financial planning.
Can I use the same equipment estimate across different projects?
Not always. Terrain, climate, and project duration vary. Customize your equipment cost estimate for each job to avoid under- or over-budgeting.
STACK’s flexibility and ease of use make it an essential tool for contractors looking to gain a competitive edge in their estimating process. By centralizing all cost data—including equipment expenses—within a single platform, STACK helps improve accuracy, efficiency, and profitability.